For almost 40 years, Minetek has been at the forefront of delivering cutting-edge engineering and technological solutions to the mining industry. Our commitment to excellence has driven us to continuously innovate industrial power systems, guaranteeing reliable performance across various sectors.
We provide a range of advanced solutions, including motor starter ancillaries, distribution, switch room, and substation capabilities. We’re proud to offer bespoke engineered power solutions that not only meet but exceed our clients’ unique needs.
At Minetek, we prioritise safety and reliability. Our solutions are built to endure the toughest operational environments, guaranteeing continuous performance and security for our partners. From ensuring smooth power distribution to protecting essential equipment, our solutions are crafted to maximise efficiency and reduce downtime.
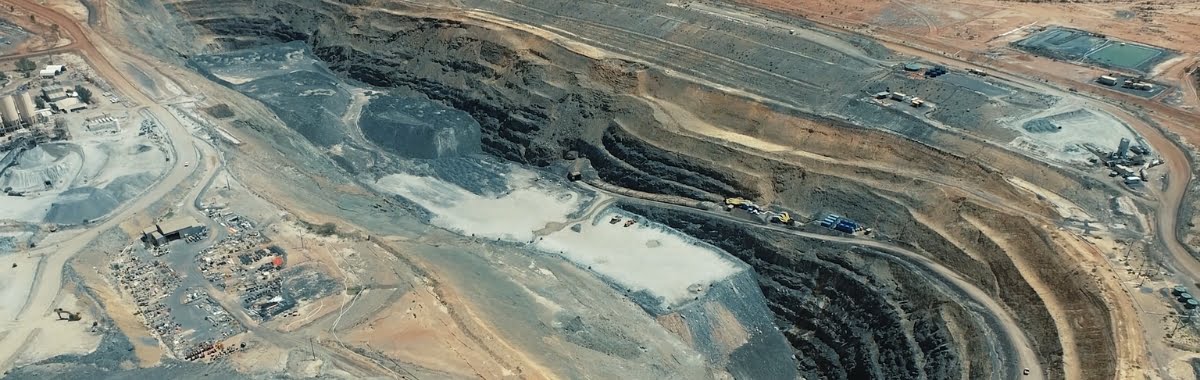
At the core of what we offer lies our diverse array of Motor Starters, each carefully designed to provide outstanding performance and flexibility. From Fan Starters to Pump Starters and Jumbo Starters, we have solutions for every need. In today’s article, we’ll dive into these various Motor Starters, exploring how they can boost efficiency, enhance safety, and simplify operations in the mining industry.
Minetek’s Motor Starters
Fan Starters
Minetek’s Fan Starters are engineered specifically for the challenging conditions of underground mining, delivering robust protection and precise control over ventilation operations, including secondary, booster, and auxiliary fans.
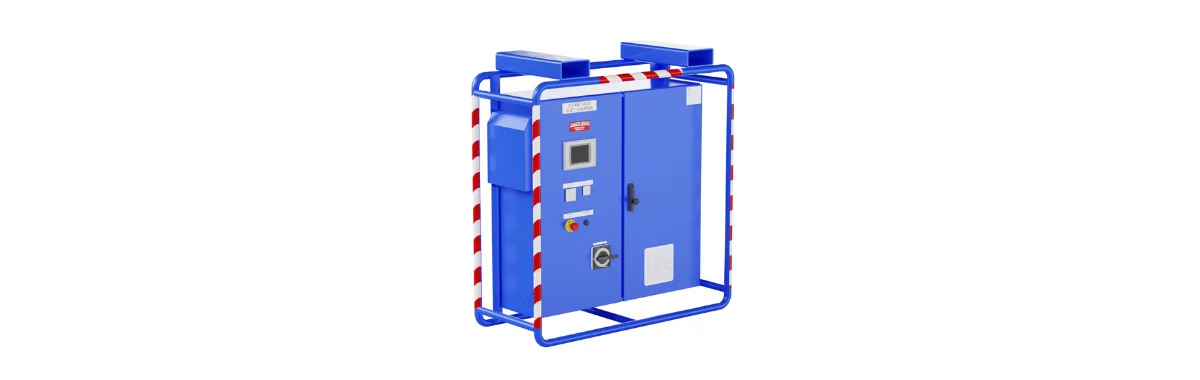
Our Fan Starters come in a tough, impact-resistant design that can be easily mounted or installed in a hanging frame. This gives underground operators the assurance of their durability and reliability. They support voltage ranges from 415V to 1000V to fit the diverse electrical and ventilation systems found in mining operations. With capacities from 55kW to 1100kW, these starters feature built-in automation that simplifies ventilation control. We also offer optional soft starters, direct online (DOL) starters, and variable speed drive (VSD) configurations for precise control and enhanced energy efficiency, ensuring they meet your specific operational needs.
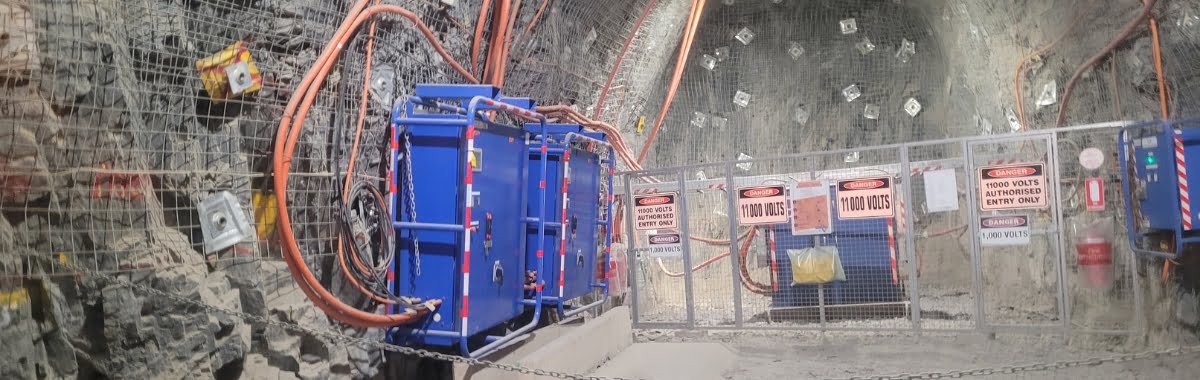
Minetek Power proudly holds ISO 9001 certification, underscoring our commitment to maintaining the highest quality standards in our Fan Starters. Designed and manufactured in Australia using premium materials, our Fan Starters can integrate with the Minetek ventilation system, providing a dependable turn-key solution for mining operations.
Beyond delivering new Fan Starters, we offer a full range of services, including programming for Motor Control Centres (MCC), Soft Starters, and PLC integration through our Performance On Demand (POD) control system. Our team collaborates closely with clients to ensure seamless integration and optimise the performance of our ventilation systems within their mining operations.
Pump Starters
Minetek’s Pump Starters are designed to ensure pumps operate reliably and efficiently across various industrial settings. With a key focus on optimising pump performance and minimising downtime, our pump starters offer practical benefits aimed at improving operational efficiency.
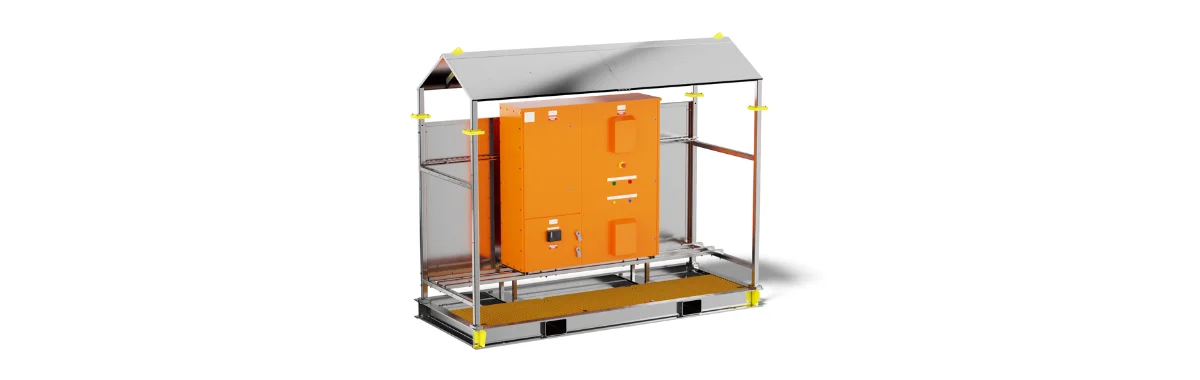
Our Minetek Power Pump Starters are built to last, housed in durable, impact-resistant cabinets that stand up to tough industrial and mining environments. Designed for easy mounting or hanging installation, they integrate seamlessly into your existing infrastructure. With support for voltage ranges from 415V to 1000V, our Pump Starters fit a variety of electrical systems typically used in industrial and mining applications. Available in power ratings from 55kW to 1100kW, they offer precise control and optimal performance for your pump operations.
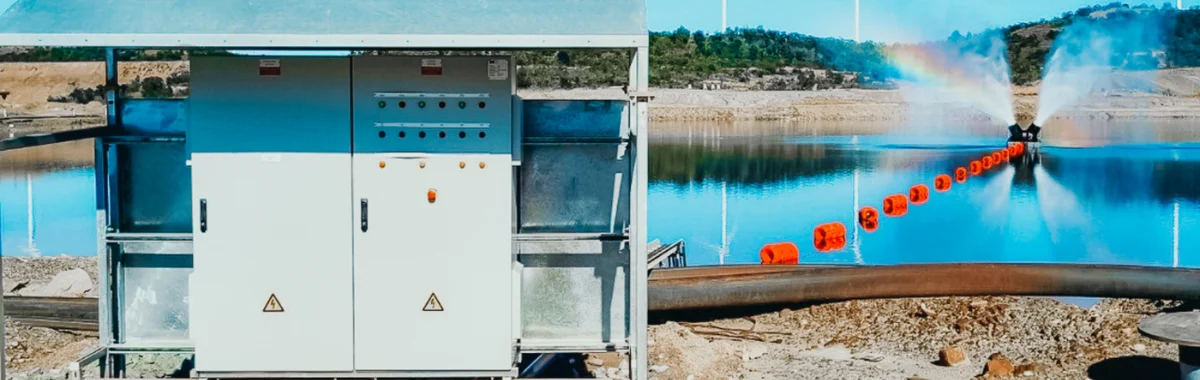
Minetek Power Pump Starters come equipped with built-in automation features, making pump system control and operation a breeze. Just like our Fan Starters, we offer optional Soft Starters, DOL Starters, and VSD options, so you can choose the control mechanism that best suits your needs. These features help ensure efficient power use, lower energy consumption, and drive enhanced pump performance.
Understanding that each industrial application is unique, Minetek Power offers Pump Starters that can be customised to Form 4 standards, with an optional 24DC control voltage for seamless integration with your existing communication system.
Jumbo Starters
Minetek Jumbo Starters are designed to operate in the most demanding underground environments, particularly in hard rock mining and tunnelling applications. These starters stand as a testament to our unwavering commitment to delivering top-tier motor control and electrical protection for heavy drilling equipment, assuring both operational efficiency and personnel safety.
In the tough and strenuous conditions of underground mining and tunneling, reliability is essential. Minetek Power Jumbo Starters are designed to deliver top-tier performance, offering strong motor control and complete electrical protection. This ensures heavy drilling equipment starts safely and efficiently, boosting productivity and ensuring smooth operations.
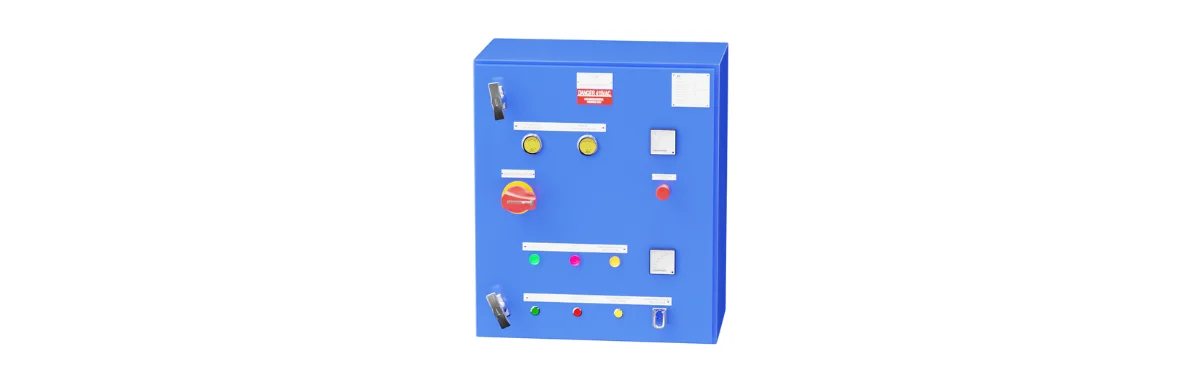
Built to withstand the harsh conditions prevalent in underground settings, our Jumbo Starters are encased in impact-resistant cabinets. This design not only protects the equipment from potential damage due to environmental factors but also ensures its longevity, minimising the need for frequent maintenance or replacement.
One of the standout features of Minetek Power’s Jumbo Starters is their versatility. They come with push button start mechanisms, giving operators an easy and intuitive way to start the equipment. Additionally, these starters can seamlessly integrate into the automation systems, allowing for centralised control and coordination within the mining or tunnelling infrastructure.
Minetek Power understands that every operation is unique, which is why we offer both manual and automated control options. Whether operators like a more hands-on approach or want to enhance efficiency through automation, our Jumbo Starters provide the flexibility to suit any operational scenario.
Minetek Power’s commitment to innovation in mining operations
These Motor Starters are more than just components. They reflect Minetek Power’s commitment to innovation and excellence. With each solution, we redefine what’s possible in the mining industry, empowering our partners with the tools they need to succeed.
As we continue to push the boundaries of innovation, Minetek Power remains dedicated to our mission to empower mining operations with transformative solutions that drive efficiency, safety, and sustainability.