Pada masa-masa awal penambangan, operasi relatif sederhana, dan sistem ventilasi terutama dirancang untuk mengalirkan udara dalam jumlah besar ke pekerja bawah tanah. Poros ventilasi dan kipas angin merupakan standar, beroperasi dengan cara yang sederhana untuk menyediakan udara segar sekaligus membuang gas-gas berbahaya. Namun, sistem awal ini kurang fleksibel - sistem ini tidak dapat dengan mudah beradaptasi dengan perubahan tata letak atau aktivitas tambang, sehingga menyebabkan ketidakefisienan.
Seiring dengan kemajuan teknologi pertambangan, begitu pula dengan kompleksitas operasi. Tambang menjadi lebih dalam dan lebih rumit, dengan berbagai tingkat dan jaringan terowongan yang luas. Kedalaman yang semakin dalam ini menimbulkan tantangan baru, termasuk peningkatan suhu, konsentrasi gas berbahaya yang lebih tinggi, dan kebutuhan akan ventilasi yang lebih canggih untuk menjangkau area tambang yang terpencil dan kompleks. Apa yang dulunya merupakan tugas sederhana untuk mendorong udara ke bawah tanah berevolusi menjadi operasi yang sangat menuntut, yang membutuhkan perencanaan strategis dan penyesuaian aliran udara secara real-time untuk memastikan keselamatan dan efisiensi.
Dengan tuntutan yang terus meningkat ini, sistem ventilasi harus berevolusi. Tambang tidak hanya membutuhkan pasokan udara yang lebih besar, tetapi juga sistem yang mampu secara aktif mengontrol di mana dan kapan udara dialirkan. Solusi ventilasi modern diperlukan untuk merespons secara dinamis terhadap pergeseran aktivitas pertambangan, beradaptasi dengan fluktuasi suhu, dan secara efektif mengelola emisi dari mesin dan operasi peledakan.
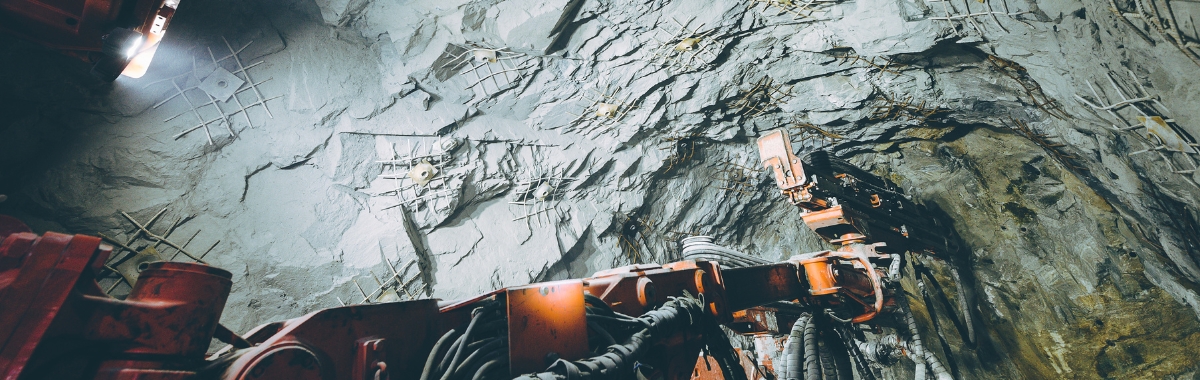
Pergeseran ke arah kontrol ventilasi waktu nyata
Transisi menuju sistem ventilasi yang lebih canggih ini bukan hanya sebuah kemajuan teknologi-ini menjadi sebuah keharusan untuk memastikan keselamatan para pekerja bawah tanah. Kemampuan untuk merespons dengan cepat terhadap kondisi yang berubah, seperti lonjakan gas berbahaya yang tiba-tiba atau penurunan kadar oksigen, memberikan tingkat keamanan yang tidak dapat ditawarkan oleh sistem sebelumnya. Hal ini mencerminkan komitmen industri yang tak tergoyahkan terhadap keselamatan pekerja.
Namun, kemajuan tersebut juga memiliki tantangan tersendiri. Tambang masa kini harus secara hati-hati menyeimbangkan penyediaan aliran udara yang memadai untuk menjaga keselamatan pekerja sekaligus mengelola konsumsi energi. Lingkungan tambang modern sangat luas, dengan zona aktif dan tidak aktif, yang masing-masing membutuhkan tingkat ventilasi yang berbeda pada waktu yang berbeda. Selain memasok udara segar, sistem ventilasi juga harus mengelola gas buang dari mesin bertenaga diesel, mengontrol panas yang dihasilkan oleh peralatan dan batuan di sekitarnya, serta meminimalkan distribusi debu.
Tindakan penyeimbangan ini semakin diperumit oleh ventilasi yang merupakan salah satu aspek yang paling boros energi dalam operasi penambangan. Di pertambangan dalam, ventilasi dapat mencapai jumlah yang menakjubkan 42% hingga 49% dari total konsumsi energi. Dengan meningkatnya biaya energi, perusahaan pertambangan menghadapi tekanan untuk mengurangi jejak energi mereka tanpa mengorbankan keselamatan.
Peraturan yang lebih ketat dan dorongan untuk keberlanjutan
Perusahaan pertambangan juga tunduk pada peraturan yang semakin ketat, dengan pemerintah dan badan-badan industri yang memberlakukan batas paparan kerja yang lebih ketat untuk gas, debu, dan kebisingan. Konsentrasi gas berbahaya yang diperbolehkan telah dikurangi secara signifikan, sementara tingkat kebisingan harus tetap berada di bawah ambang batas yang ditetapkan untuk melindungi pendengaran pekerja. Meskipun kesehatan dan keselamatan pekerja selalu menjadi prioritas utama, peraturan saat ini menuntut ketelitian yang lebih tinggi dalam memantau dan mengendalikan kondisi bawah tanah. Akibatnya, sistem ventilasi tidak hanya harus kuat tetapi juga sangat mudah beradaptasi dan presisi.
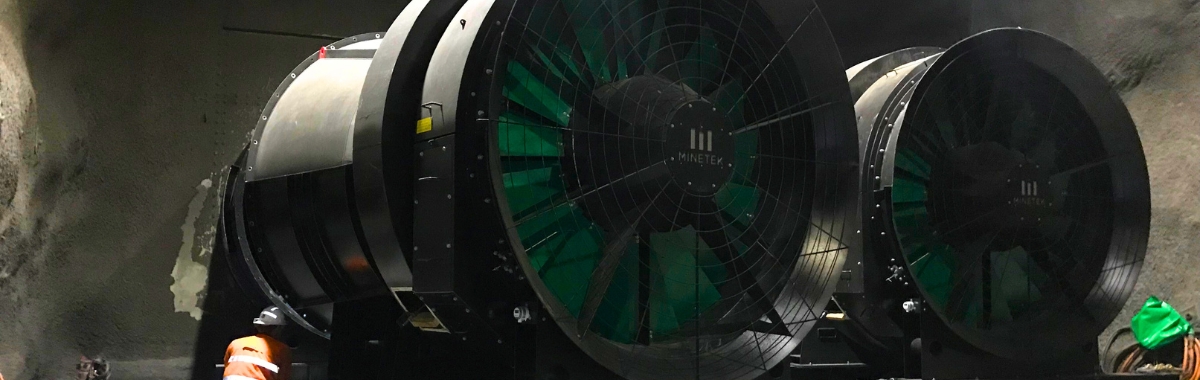
Pada saat yang sama, industri pertambangan menghadapi pengawasan publik dan investor yang semakin ketat, sehingga mendorong penerapan praktik-praktik yang lebih berkelanjutan dan ramah lingkungan. Alih-alih menolak perubahan ini, industri ini justru merangkul inovasi. Operasi pertambangan diharapkan dapat mengurangi emisi karbon, menurunkan konsumsi energi, dan beroperasi dengan jejak lingkungan yang lebih rendah. Tuntutan ini telah mendorong kemajuan yang signifikan dalam teknologi ventilasi, yang mengarah pada pengembangan solusi yang lebih hemat energi dan cerdas. Pendekatan proaktif industri terhadap keberlanjutan merupakan indikator positif bagi masa depan pertambangan.
Salah satu inovasi yang paling menjanjikan dalam bidang ini adalah Ventilasi Sesuai Permintaan (VOD). Sistem canggih ini merevolusi manajemen aliran udara di tambang bawah tanah. Tidak seperti pengaturan ventilasi tradisional yang mengalirkan aliran udara secara konstan ke seluruh tambang, VOD memanfaatkan sensor untuk mendeteksi di mana dan kapan udara segar dibutuhkan, serta menyesuaikan aliran udara. Pendekatan yang dioptimalkan ini tidak hanya meningkatkan efisiensi energi, tetapi juga menyediakan lingkungan kerja yang lebih aman dan nyaman bagi para penambang.
Bagaimana Minetek Air mendefinisikan ulang standar industri
Contoh utama dari VOD yang sedang beraksi adalah Teknologi Mine Air Control (MAC) dari Minetek. MAC menggunakan sensor canggih dan pelacakan RFID untuk memantau pergerakan personel dan mesin di seluruh tambang. Berdasarkan data waktu nyata ini, sistem secara otomatis menyesuaikan ventilasi untuk memastikan udara segar diarahkan tepat ke tempat yang dibutuhkan, sehingga tidak perlu lagi ada intervensi manual. Manajemen aliran udara yang cerdas ini tidak hanya memastikan ventilasi yang optimal di area-area kritis, tetapi juga meningkatkan produktivitas dengan memungkinkan para penambang untuk fokus pada tugas-tugas penting.
Dengan terus merespons kondisi bawah tanah, MAC dan sistem serupa memungkinkan pendekatan yang lebih adaptif dan efisien untuk ventilasi tambang. Misalnya, jika zona tertentu tidak dihuni atau tidak aktif, sistem dapat mengurangi aliran udara ke area tersebut, menghemat energi dan memperpanjang masa pakai peralatan ventilasi. Pendekatan sesuai permintaan ini secara signifikan mengurangi biaya operasional sekaligus meningkatkan keselamatan pekerja secara keseluruhan.

Salah satu inovasi Minetek yang paling inovatif adalah Teknologi Performance on Demand (POD). Secara tradisional, sistem ventilasi tambang mengandalkan Variable Speed Drives (VSD) untuk menyesuaikan kecepatan kipas, yang menawarkan beberapa tingkat fleksibilitas tetapi juga menghadirkan keterbatasan. Teknologi POD Minetek menghilangkan kebutuhan akan kontrol VSD sama sekali, memungkinkan penyesuaian aliran udara langsung tanpa bergantung pada kontrol kecepatan perantara.
Pendekatan generasi berikutnya ini memastikan bahwa aliran udara diatur dengan tepat-menghasilkan apa yang dibutuhkan, tidak lebih dan tidak kurang-menghasilkan sistem yang sangat efisien. Ketepatan teknologi POD memungkinkan tambang mempertahankan ventilasi yang aman dan efektif sekaligus mengurangi konsumsi energi secara signifikan. Bahkan, metode ini dapat mencapai penghematan energi hingga 50%, menawarkan pengurangan biaya yang substansial sekaligus mendukung tujuan pelestarian lingkungan. Dengan menyelaraskan diri dengan gerakan yang lebih luas menuju praktik pertambangan yang lebih ramah lingkungan, teknologi POD menggarisbawahi kelayakan ekonomi dari keberlanjutan dalam industri ini.
Dengan kemajuan seperti MAC dan POD, Minetek Air menetapkan tolok ukur baru untuk efisiensi, keamanan, dan keberlanjutan dalam ventilasi bawah tanah. Teknologi ini tidak hanya menjawab tantangan yang paling mendesak dalam industri ini, tetapi juga membuka jalan bagi masa depan pertambangan yang lebih inovatif, hemat biaya, dan bertanggung jawab terhadap lingkungan.