Australia’s abundant reserve of minerals and rare earths has made mining one of the country’s most established sectors [1]. As one of the largest mining countries in the world, the mining industry has always been crucial in Australia’s development and economic growth, with mined natural resources equating to 70.7% of Australia’s exports in 2022 [2].
While the industry deals with metals production, investing, and trading, the act of mining itself often refers to the extraction of precious metals and minerals from the ground. To accomplish all this, mining operational sites require a range of different mining machinery and equipment.
When working on a mining site, it is important to have efficient mining machinery and equipment that directly aids an increase in production and operations. There is a variety of machine types and models designed specifically for the mining industry across OEMs, such as Ulat, Liebherr, Komatsu, and Hitachi. This article discusses the primary models of machinery and equipment used in mining operations both in Australia and around the world.
1. Excavators
Mining excavators are used for digging raw materials and are particularly useful for surface mining. Armed with powerful lifting arms and huge buckets with large capacities, these machines are capable of excavating huge amounts of materials. They are one of the most crucial pieces of equipment due to their versatility, manoeuvrability, and multi-functionality. Excavators can perform tasks with minimal errors and are much more efficient than manual labour, hence reducing the need for human labour and increasing profitability.
One of largest mining excavators in the world is the Liebherr R9800, which can move up to 240 000 cubic metres of dirt and rock per day. Other huge excavators include the Hitachi EX8000-6 and the Komatsu PC8000-6.
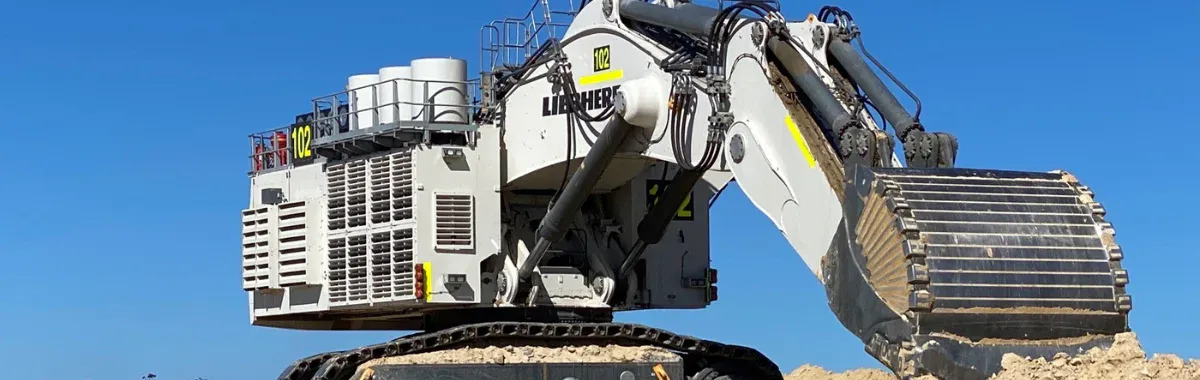
2. Dump Trucks
Dump trucks, also known as haul or tipper trucks, are widely used across the mining industry for the handling of heavy materials. These trucks are used around mining sites to transport materials and mined minerals and are equipped with an open-box hinged at the rear, which can be used for handling and dumping materials.
Dump Trucks are built to work in harsh working conditions with large tires that can support their heavy loads over uneven terrains and large beds that can carry a wide range of materials. Dump trucks increase efficiency by easily and efficiently transporting materials across mining sites as needed.
Some popular dump truck models include the Caterpillar 793 or the Caterpillar 775G, the Liebherr T 284, and the Komatsu 960 E-1.
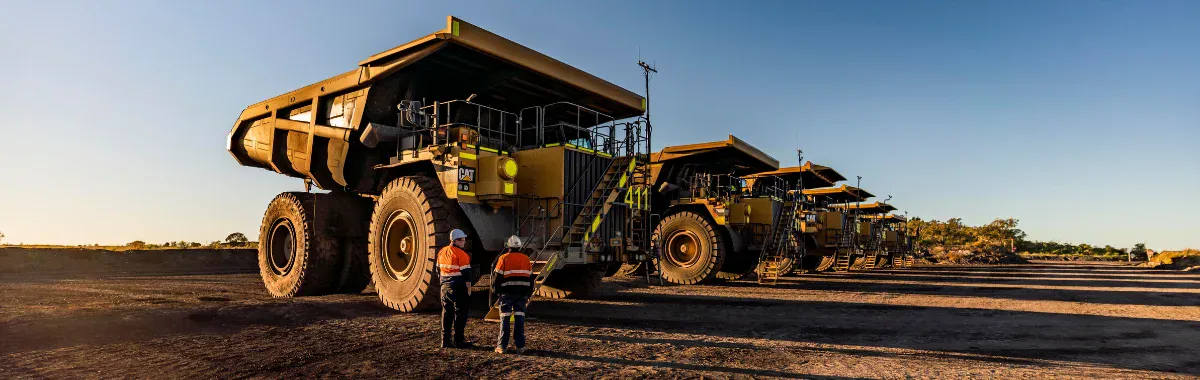
3. Dozers
A bulldozer is a tractor with a heavy blade for pushing and excavating earth and debris at mines. Ripping with a dozer has become a popular method to loosen soil when blasting is not an option – which is of particular importance, with local authorities introducing restrictions surrounding blasting operations too close to towns and cities. Ripping with a powerful bulldozer is also considerably cheaper than a combined drilling/blasting operations.
The most common bulldozers in mining are wheel dozers and crawler dozers. Crawler dozers, or tracked dozers, are typically the dozer of choice for many mining sites due to their weight-to-horsepower ratio to push large loads. However, wheel dozers have become increasingly popular, as their speed and versatility make them easier to quickly manoeuvre around mining sites.
The biggest dozer in production now is the Komatsu D575A-3SD, but other huge dozers that are popular include the Caterpillar D11T and the new release, the Komatsu D475A-8. In terms of hydrostatic dozers, the biggest one is the Liebherr PR 776.
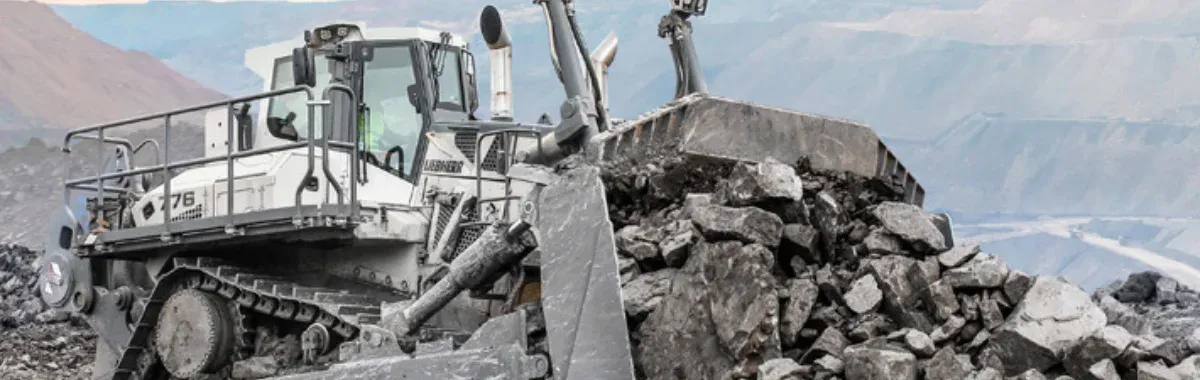
4. Wheel Loaders
Wheel loaders are a piece of heavy equipment capable of lifting almost anything, such as debris, gravel, soil, dirt, pallets, and more. Aside from earthmoving purposes, wheel loaders are versatile equipment that can be used in different applications, such as loading materials onto trucks or other machinery for transporting.
In mining, wheel loaders are a reliable piece of equipment. The carrying job is done by operating the bucket, usually located at the front but sometimes at the back of the vehicle. This bucket can move up and down, depending on the requirement. While capacities differ according to classes, wheel loaders generally have high capacities, and compared to an excavator, a wheel loader is easier to operate, attributed to the fact that the latter has more mobility.
Caterpillar wheel loaders have been the most popular within the mining industry, with a wide range of compact, small, medium, and large loaders. The Caterpillar 966E and Komatsu WA1200-6 are particularly renowned.
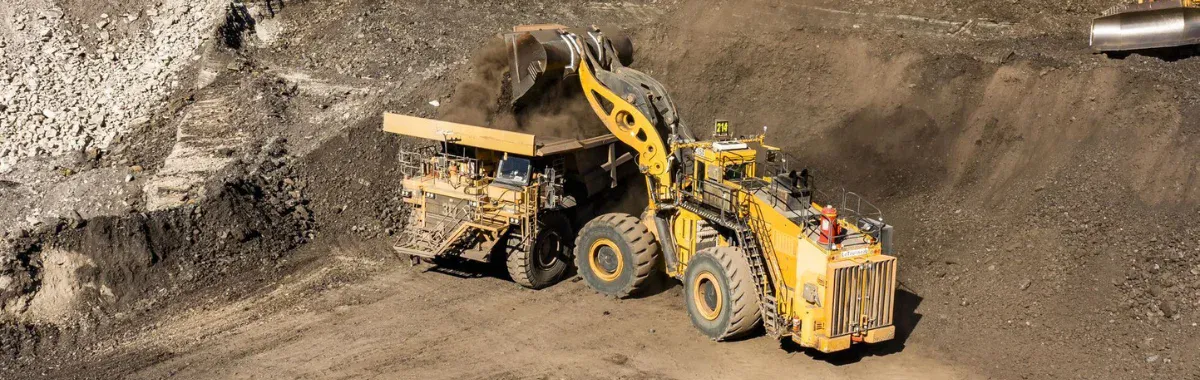
5. Drill Rigs
Drill rigs are commonly used in mining sites for drilling holes in rock or soil. In surface mining, holes are usually drilled for the placement of explosives so that ores near Earth’s surface can be removed and carried to refineries to extract the minerals.
Rotary drill rigs are the most versatile and effective. Their lightweight modular design makes the drilling rigs easy to install and relocate, allowing for greater operational flexibility. Compared with traditional drilling rigs, a rotary drilling rig has high torque and can automatically adjust itself according to strata. They are much quicker than other drills on the market — reaching ten mph in soil and sand and 4–6mph in clay soil (3–5 times faster than conventional drilling rigs).
The Komatsu 77XR rotary drill was recently introduced in 2016 and is designed for blasthole drilling for a range of materials from coal to hard rock.
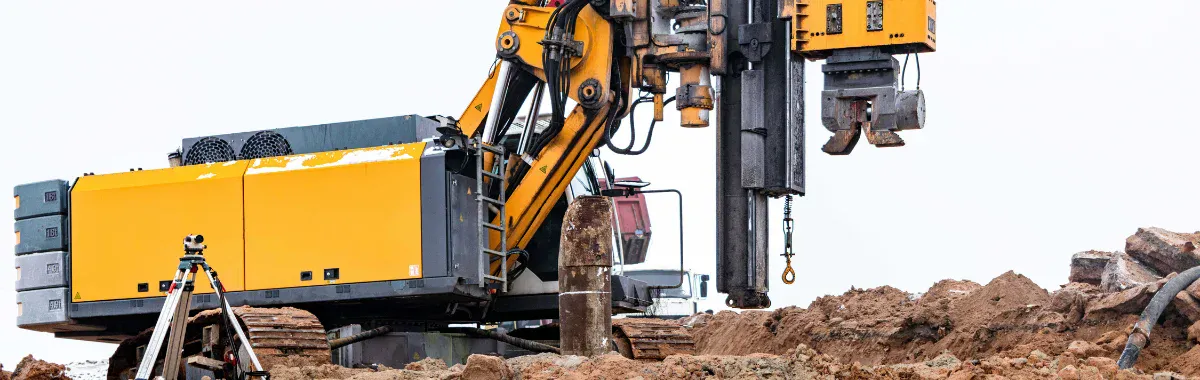
6. Water Trucks
Water trucks are crucial to mining operations by helping with dust suppression and even fire control. A water truck is necessary on most mining sites because of the various safety and health risks that respirable dust particles pose. Excessive dust can lead to serious health concerns for miners, such as pneumoconiosis (CWP), a potentially disabling lung disease. In Queensland, coal mining regulations limit workers’ exposure to respirable dust. Dust can also impact productivity at the sites when workers cannot see clearly through clouds of dust. Furthermore, dust emissions have many negative impacts on the environment.
Caterpillar’s newly launched 777G Water Solutions truck aims to help solve overwater and underwatering issues while tackling sustainability.
The Importance Of Efficient Mining Equipment
This range of machinery and equipment are used to ensure efficiency and success in mining operations worldwide. However, one common issue with such heavy machinery is the level of noise that comes with utilising such machines. The noise pollution emitted by these loud machines can be dangerous and detrimental to workers’ health.
Specialising in equipment such as trucks, diggers, excavators, drills, loaders, dozers and more, Minetek has attenuated over 1,200 mining machines across more than 90 different OEM-approved models. Our solutions have been proven to reduce mining noise by as much as 50%, enabling mining operations to reduce potentially harmful safety impacts on operators and meet regulatory and community noise expectations.
Recognised globally as an innovative and technology-driven solutions provider, Minetek has over 30 years of experience providing sound, water, and air solutions to mining companies worldwide. Our sound attenuation solutions ensure large mobile machinery meet all relevant compliance laws, saving operators considerable amounts of money in the process.
References
- International Trade Administration – https://www.trade.gov/country-commercial-guides/australia-mining
- Reserve Bank of Australia – https://www.rba.gov.au/snapshots/economy-composition-snapshot/pdf/economy-composition-snapshot.pdf
The team at Minetek are confident and ready to provide solutions that match your needs. Contact us to find out more about our machinery noise reduction packages.